10 Cost-Cutting Strategies for Cleanrooms
The high-end technicalities of a cleanroom make the cost associated with it considerable. As some industries cannot afford to exist without a cleanroom system, they must strategize with practical cost-cutting strategies.
Appropriate planning, behavior of operators, and proper usage of equipment largely determines the maintenance cost of cleanroom solutions. On the other hand, space area, cleanliness level and an efficient HVAC system determine its initial construction cost.
In this blog post by ACH Engineering, let us look at 10 cost-cutting strategies for cleanrooms that reduce cleanroom construction and maintenance costs without compromising industry codes, standards, and most importantly, the intent of the cleanroom operations.
1. Optimizing HVAC System Design
Heat generated by the AC compressor creates increased burden on the cleanroom HVAC system and dumps heat around your cleanroom area. This impacts the performance of both AC and HVAC systems, thereby jeopardizing the low ambient air temperature requirement of the cleanroom.
Here comes the role of ventilation fans and exhaust ducts in cleanrooms. Installing ventilation fans and exhaust ducts releases hot air from the cleanroom, thereby safeguarding the AC and HVAC system. Further, installing a recirculation system and ducting controls that sends the exhaust air to the AC before reaching the fan filter units (FFUs) ensures that no hot air is released within the cleanroom system.
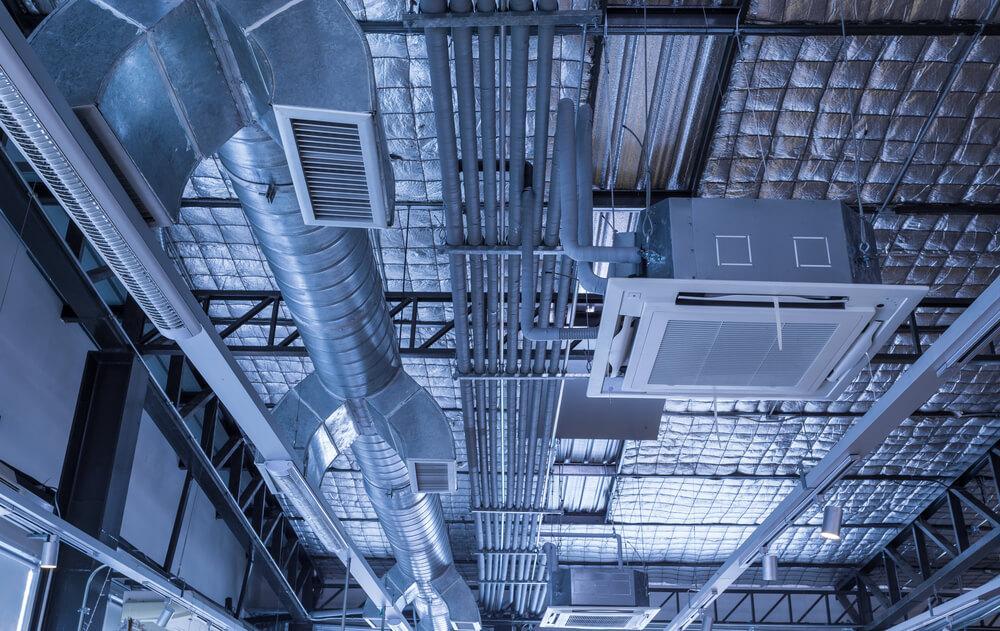
2. Map the Size of Your Cleanroom
Always opt for the cleanroom size that you actually need considering your process/operational requirements. You can expand your cleanroom area whenever you want. Since the inception of modular cleanroom, disassembling and reassembling of cleanrooms have become so much easier with ACH Engineering, a top choice among cleanroom services in Ontario.
Those who invest in a larger cleanroom than is required also have to bear extra maintenance costs related to electricity, filters, equipment and so on.
3. Plan the Cleanroom Lighting
Steep electricity bills due to elaborate cleanroom lighting are often a complaint from the ACH Engineering clients. As a solution we always recommend opting for LED cleanroom lighting options, which do not affect the laminar flow in the cleanroom area.. These can easily be applied on the cleanroom ceiling with a degree of output that is the same as fluorescent lights. LED cleanroom lights offered by ACH Engineering last 10 times longer and save more than 55% of energy cost compared to traditional fluorescent lighting units.
4. Use Auto Control Fan Filter Units (FFU)
When designing a cleanroom, there are two choices:
- AC Fan Filter Unit (using Alternate Current)
- DC Fan Filter Unit (using Direct Current)
Among the two, ACH Engineering always recommends the DC Fan Filter Unit because of its low recurring cost. DC units cost more than AC units initially, but over time, lowered maintenance costs make DC units a better choice.
Another popular alternative as a practical cost-cutting strategy for cleanrooms is the use of room-side replaceable (RSR) fan filter units. For most cleanroom applications, RSR units simply the filter replacement process, reducing downtime and other financial burdens. Opting for FFU units that maintain the cleanroom-controlled environment to its right ISO level, will help you keep an eye on the total cost of the ownership (Initial cost + Service cost + Energy cost).
5. Add a Pass-thru Chamber
Pass-thru chambers are becoming inevitable in today’s cleanroom designs. There are 3 benefits of pass thru chambers for cleanrooms – low associated energy cost, control pressure differential fluctuations and optimum productivity.
Much smaller than cleanroom doors, pass-thru chambers allow transferring supplies into the cleanroom with minimal human interaction, thereby diminishing any scope for contamination due to foot traffic.
6. Encourage Healthy Cleanroom Practice
Operators in the cleanroom are the biggest source of contamination. A single action from an operator can produce major contamination leading to additional financial expenses. Thus, it is important to train every operator who enters, spends time, or works in the cleanroom. In the post-pandemic era, it is very important to restrict the entry of operators with symptoms of illness. Ensuring that every operator in the cleanroom adheres to the same sanitization, gowning and cleanliness standards will help to maintain a safe environment in the cleanroom.
7. Cleanroom Filtration Process
Regular filter maintenance of cleanrooms alone can reduce expenses to quite an extent. To support the cleanroom specification, we recommend installing 3 kinds of filters – HEPA, bag/box filters and pre-filters. Both HEPA and bag/box filters are time-consuming and expensive to replace. Thus, ACH Engineering as a leading cleanroom solutions provider in Canada recommends frequently changing the cleanroom pre-filters as they are low in cost and protect both HEPA and bag/box. Pre filters with high dust holding capacity increase the lifespan of both HEPA and bag/box filters.
8. Classified Cleanroom Cleaning
Haphazard cleaning of your cleanroom can take a toll to your operational cost. Haphazard cleanroom cleaning also leads to an accumulated waste of resources and a compromised productivity. Here the solution is to opt for an experienced turnkey cleanroom solutions provider such as ACH Engineering who can do the cleanroom cleanliness meticulously in time and in short budget. Cleanrooms being highly sensitive should not be experimented with. In Canada, ACH Engineering is counted among the best controlled environment and cleanroom service providers.
9. Opting for Softwall Cleanrooms for Temporary Projects
When planning for a cleanroom on a tight budget, try going for softwall cleanrooms over cleanroom wall panels. Softwall cleanrooms are budget-friendly, low cost and are currently available in many designs. Softwall cleanrooms can also be easily relocated with braked casters. These are lightweight and hence, easy to install anywhere and everywhere. Softwall design works for both traditional and modular cleanrooms.
10. Turning Down the Cleanroom
Reducing the frequency of air in a cleanroom is called turning down the cleanroom. When the particle count in a cleanroom is consistently lower than the standard, it requires reduction in the number of air changes. This reduction in the number of changes leads to major cost-cutting. Reducing the frequency of air in a cleanroom should be done in accordance with cleanroom ISO standards, and without harming the ongoing cleanroom processes.
The aforementioned are 10 cost-cutting strategies for cleanrooms that can be applied without impacting the workflow of the cleanroom. These 10 cost-cutting strategies for cleanrooms have been tried and tested in diverse industries, and are highly recommended by ACH Engineering, offering modular cleanroom services in Ontario, Canada with the fastest and most economical construction methodologies.
GET IN TOUCH
Complete the form below to get in touch with our team.