Introduction to Cleanroom Coving
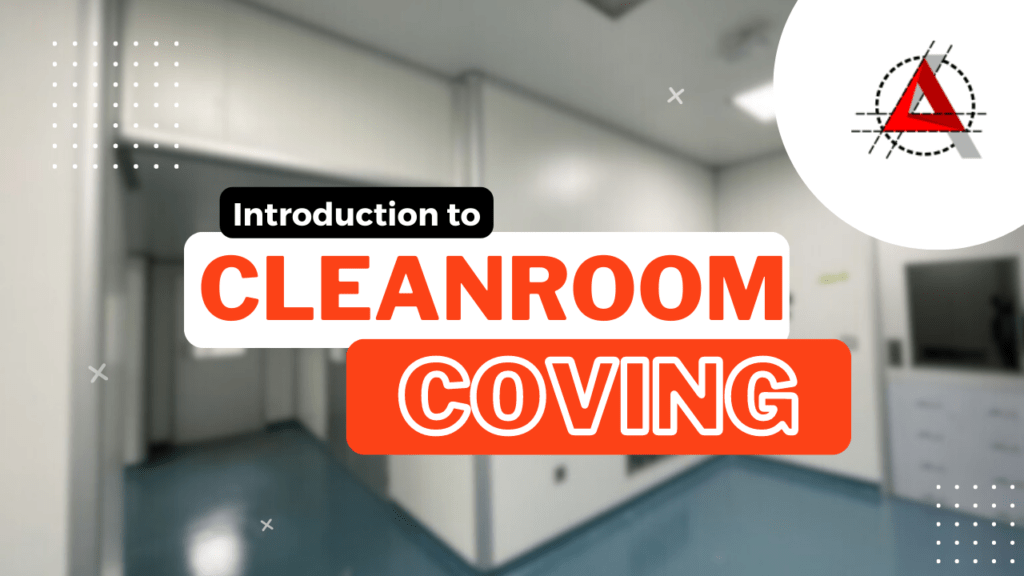
Cleanrooms are vital spaces for both pharmaceutical and specialized industries, where compliant manufacturing products are generated. In these rooms, the close control of production conditions is required to ensure high-quality output that satisfies industry guidelines. The levels of pollutants, particles, and any other potential contaminants must be kept to a certifiable minimum. In order too successfully achieve this controlled environment, all aspects of the design and operation of the space is optimized to carefully reinforce control and accountability. Let’s take a look at one aspect of cleanroom designing: coving.
What is Coving?
A coving is a piece of material that has been fitted to cover the seam or transition between two surfaces, such as the edge between two walls or between a wall and the ceiling or floor. It can install a radius (when it is curved) or a 45° angle instead of the traditional 90° of a room’s corner.
In cleanrooms, coving is required for use to make sure that corner transitions are fully flush and seamless with no sharp corners present, because this helps reduce material buildup and simplifies regular cleaning. From pharmaceuticals to food processing, clinical laboratories through other sterile environments, coving helps make cleanrooms effective and easy to maintain.
Why is Coving Needed?
Current good manufacturing practices (cGMP) requirements specify the need for coving, and so facilities must install it to be compliant and maintain sterile work environments. The reasons behind these requirements have everything to do with minimizing the risk of contaminant accumulation and maximizing the capacity for regular cleaning of the space. The effectiveness of these efforts depends on the build, geometry, and materials used inside of the rooms.
What is wrong with 90°? By eliminating 90° corners, coving prevents the typical accumulation of dust particles, dirt, bacteria, and other debris. Well-installed coving keeps water or other chemicals from building up in the walls. It is also easier to thoroughly clean coving, both because the materials are designed to withstand regular cleaning and because the shape is more conducive to a deep clean than a right-angled corner.
Eliminating corners also streamlines the pathways for air flow in these rooms, which helps regulate air flow, temperature control, humidity, and pressurization.
Coving Material
Coving is commonly made of metal, aluminum, plaster, or plastic, depending on specific institutional guidelines. It can be treated or covered to further increase compliance; for example, ACH Engineering offers aluminum coving that is powder coated, as well as aluminum anodized coving. These materials are designed to withstand constant, regular cleaning.
Silicone edges are common to facilitate an airtight seal.
Benefits of Different Materials and Finishes
Each of the different materials and finishes offers different benefits. Some common coving materials includes:
- Aluminum is a good choice if impact or corrosion resistance is a concern, and it is easy to add on additional finishes to help further augment its strengths.
- PVC can be reinforced with materials like glass or metal, while its surface can resist intense and frequent cleaning.
- Polystyrene is the lightest coving solution, with the least impact on your budget. Unfortunately, it is also the most prone to damage and therefore not an adequate cleanroom solution without additional reinforcement.
- Wood finishes are typically used for aesthetic reasons, and less for laboratory functionality. Even when sealed, wood coving does not withstand the wear-and-tear inherent to cleanroom environments.
- Plaster was the traditional solution before contemporary alternatives emerged. While plaster is effective in applications like building restoration, it is heavy and brittle.
- Hardened polyurethane is affordable, lightweight, and easy to install in a highly customized manner since it can bend around windows and other decorative elements. Unfortunately, it’s not considered to be a very durable material.
As already mentioned, a range of finishes are available to further adapt materials so that they can withstand particular conditions. Powder coating uses an electrostatic charge to affix a powder to a surface, effectively hardening it so that it can be more resistant over time and heavy use. Aluminum anodizing surfaces is an alternative that can confer corrosion resistance and improve adhesion without altering the strength of the surface.
What Happens if Coving is not Secure?
If coving is not secure, the integrity of its installation can easily become compromised, which results in its protective properties being limited.
The coving is designed to be chemically resistant, helping it withstand not only daily cleanroom functions but also regular cleaning. And even though protocols call for daily cleaning, that cleaning is more effective and easier to execute with coving in place. The lack of seams that results from properly installed coving helps to prevent any contamination from biological agents, chemicals, or other agents. If coving is not secure, contamination and build-up can occur.
Usually, coving is designed to be thermally resistant as well, so that it can accommodate some fluctuations in temperature without facing changes to its structural integrity.
Common Considerations and Challenges
There are several key considerations to keep in mind when installing coving in a cleanroom.
The materials used in a cleanroom must be perfectly smooth to facilitate easy and effective cleaning without any material deposits building up. Any seals to bind the coving materials should use silicon that is FDA-approved and not prone to harboring fungi or other contaminants. All materials in a cleanroom need to be able to withstand the regular use of industrial-grade decontaminants.
There need to be channels built into the coving to accommodate utility cables and even panels, where appropriate. If anything, else needs to be inspected, the coving needs to be designed so that it can be moved easily. Air ducts and diffusers should be designed to prevent contamination and sustain regular air flow.
The surfaces on which coving is placed factor into installation considerations.
- Floor surfaces need to be non-porous, as all other surfaces in a cleanroom, to reduce the harboring of contaminants. The floor must be resistant to constant friction and potential abrasions, while also being slip-resistant. It must be able to accommodate a heavy load that is either still for long periods of time or frequently moving around, without being altered. As an extension of the floor, the coving needs to accommodate these properties as well.
- Walls must be easy to clean without absorbing any particles or chemicals. There are many fixtures integrated into a laboratory environment, and these must be sealed seamlessly to ensure easy cleaning and minimal build-up. Once again, the coving must be an extension of the properties of the wall.
- Doors need to be designed to maintain airtight seals when closed, so that air does not flow into or out of the room as that could promote cross-contamination and reduce the integrity of the cleanroom. Any coving must be perfectly flush and seamless with the doors and work together to reinforce best practices in the cleanroom.
- Lighting must also be installed flush with all cleanroom surfaces. Many lights are designed to be accessed externally from the cleanroom, so that its integrity may be maintained, and minimal disruption of the airflow can occur. Once again, coving must serve to accommodate the lighting in a way that preserves the integrity of the cleanroom’s compliance with cGMP guidelines.
GET IN TOUCH
Complete the form below to get in touch with our team.