How to Properly Clean a Cleanroom
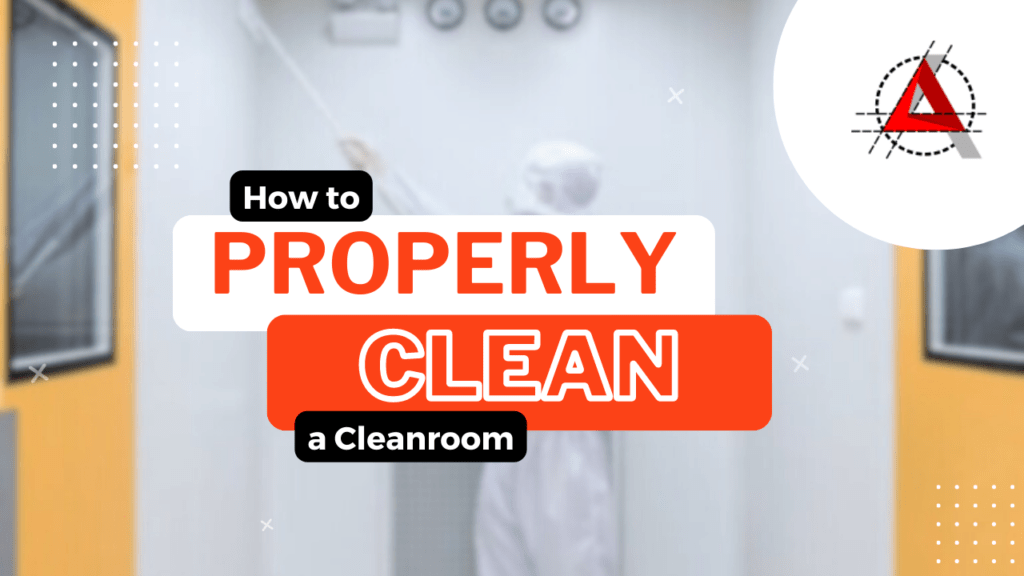
Finally, your clean room is installed and fully operational. You put a lot of time and resources into creating your perfect cleanroom. Now you can sit back and relax.
Well, yes – but the work isn’t done just yet. Any cleanroom requires constant cleaning. No matter how great your filtration systems are, there are always ways for contaminant exposure. But when adhering to proper cleaning protocols, your cleanroom will exceed your expectations for performance and longevity. Cleaning procedures for cleanrooms are different from ordinary cleaning of your house or workplace. There are many factors that one should keep in mind when working to keep a cleanroom clean. Here are some tips to help you keep your cleanroom as contaminant-free as possible.
Follow sanitation protocols when entering a cleanroom
The best way to keep your cleanroom safe and clean is to prevent contaminants from entering the room. The most significant contributor to pollutants is usually the personnel. All staff should be aware of proper sanitation protocols before entering the cleanroom. This includes washing and drying hands, wearing sterile gloves, and following proper gowning procedures. Moreover, all tools and equipment must also go through appropriate sanitation and disinfection before they’re allowed in the cleanroom.
Know your specific industry standards
Your cleanroom will have specific ISO classification and cleanliness standards depending on your industry and applications. Cleanrooms with higher ISO classifications might not need as much maintenance because of high levels of air filtration. Cleanrooms with lower ISO classifications, on the other hand, require a more frequent and more thorough cleaning routine. As air filtration is not a strict requirement, more comprehensive sanitation processes are necessary.
Two cleaning methods for cleanrooms
Dry transfer cleanroom cleaning
All you have to do is wipe surfaces in your cleanroom with a dry cloth with absorbent material when using this method. The cloth should be a cleanroom-specific kind, meaning it will not break apart, shed fibers, or redeposit contaminant particles.
Wet cleanroom cleaning
Wet cleaning is a good alternative when the dry transfer isn’t enough to remove particles. This method requires decontamination using cleaning fuel. Keep in mind that only specific non-ionic, non-foaming cleanroom-specified cleaning solutions are allowed.
Depending on the type of contamination, you can use either method. However, it is important to understand that proper cleaning often involves both practices.
Additional cleaning equipment
Indeed, there are times when basic cleaning methods are not good enough. In such a case, bringing the advanced cleaning equipment is the right call. Based on the nature of the contamination, advanced cleaning equipment may take the form of a portable HEPA filtration system that will erase the contaminants in the air. Or, it may be Dry Hydrogen Peroxide disinfection, which attacks microbes in the air and on the surfaces. Steam cleaning may also be used for deep sterilization of surfaces and laboratory equipment. Cleanroom vacuums are one the most crucial equipment to clean cleanrooms. It uses either HEPA or ULPA filters to remove contaminant particles from the cleanroom environment.
Top to bottom cleaning routine
Always start to clean your cleanroom beginning at the top – ceiling, top shelves, top surfaces of the cabinets. Even if you’re wiping surfaces with special cloths, bacteria and particles can still escape. Due to gravitation, they land on lower surfaces. Starting cleaning from the top will make sure all of the contaminating particles are cleared away as you clean the lowest surface of your cleanroom – floor. The floor is the easiest surface to obtain and spread the bacteria, so ensure you sweep and mop with proper disinfecting solutions. You might also want to invest in a shoe cleaner or sticky mats to minimize the spread of contaminants.
Regular cleanroom cleaning routine
Depending on your cleanroom ISO classification, the frequency of cleaning tasks might vary. However, specific cleaning tasks must be performed daily, weekly, and as-needed for any cleanroom. Ideally, your company will have an SOP for cleaning, which states the frequency of cleaning based on the specific chemicals and products used. The SOP will ensure cleaning and sanitation procedures are performed the same way every time.
Daily cleaning tasks
Prior to starting any work in the cleanroom each day, operators should sanitize the floor and dry it with a HEPA filter vacuum. The same vacuum must be used on the walls of a cleanroom. All the windows and pass-throughs must be washed and dried as well. At the end of the shift, staff should wipe down all the surfaces (even unused ones) with a dry or wet cloth depending on the level of impurity.
Weekly cleaning tasks
Even though the walls are being HEPA vacuumed every day, they should be cleaned with distilled water or a particular solution for deeper disinfection once a week. The same notion applies to the floors. Once a week, the floors should be moped with specific detergent and distilled water and vacuum dried after.
As-needed cleaning tasks
The following tasks should be performed at least once a month or on an as-needed basis. The ceilings should be washed with special detergents and distilled water. Light lenses should be wiped off. Depending on the machine used as a shoe cleaner, it must be deep cleaned or replaced. If you invested in sticky mats (which is a great idea!), they should also be either professionally cleaned or replaced.
Pharmaceutical cleanroom cleaning routine
When it comes to pharmaceutical cleanrooms, there is an essential difference between cleaning and disinfecting. Cleaning means the removal of buildup, grime, and dirt from the surfaces using detergent or soap. That step is followed by rinsing away loose dirt and debris. Disinfection comes after cleaning and serves the purpose of killing bacteria and microbes that weren’t removed by the cleaning process. The disinfection step sterilizes surfaces so that work can resume safely. All cleaning and disinfection supplies should be kept in a dedicated spot inside the cleanroom to minimize the possibility of contamination.
Cleaning SOP is significant in pharmaceutical cleanrooms. It includes specific guidelines about timeline and cleaning product specifications to help keep your cleanroom running smoothly. Cleaning of heavily used areas as floors and surfaces should be performed daily. In contrast, tasks like replacing air filters should be performed throughout the year at regular intervals. Before starting each shift, operators should examine the additional pharmaceutical equipment like the glove box or pill packaging systems. Depending on the equipment, it should be inspected and serviced professionally once or twice a year.
ACH’s cleanrooms are designed and built using antimicrobial and smooth materials, so that microorganism and bacteria growth risk is negligible. Moreover, all ACH products are tested for most of the harsh chemicals, and the results of their reactions are within an acceptable range.
GET IN TOUCH
Complete the form below to get in touch with our team.